3.2 - Typical Problems
Typical Pump Failure
Fuel pumps generate two types of failure: electrical and mechanical.
- First, the NO START caused by a lack of fuel in the delivery system.
- When a no-start condition occurs, the basic vital signs, including spark, fuel and compression, are to be tested. Fuel pressure reading is a must to ensure proper engine operation.
- Second, the PERFORMANCE-related conditions.
- Hard start
- Rough idle
- Hesitation
- Lack of power
- Engine misfire
- Intermittent engine performance
All of the conditions mentioned above can also be problems related to the fuel delivery.
Contaminated Fuel Tank
One of the main causes of fuel pump failure is contaminants found in the fuel tank. A vehicle can easily be refuelled over 100 times (6,000 liters/1,600 gallons) for approximately 40,000 km/26,000 miles. Contaminants comes from a variety of sources like the fuel itself, a missing fuel filler cap or one of the most overlooked components: the fuel filler tube which is, in most cases, exposed to a very harsh environment. Fuel filter replacement is another source of contaminants returning to the tank.
The fuel tank must be inspected or cleaned before installing the fuel pump. Install a new strainer filter when needed and ensure proper positioning.
Saturated Fuel Filter
The fuel filter is the main defence against dirt and water that can circulate in the system. On return-type systems, the filter will have over 10,000 gallons / 36,000 liters of fuel circulating through in a period of approximately 2 years.
After a certain time, a dirty filter will be unable to prevent dirt from circulating in the fuel delivery system and will start a slow build-up in the tank.
As the filter clogs, the fuel pump will also have to overcome the restriction. This increase in effort cause the fuel pump to run at a higher current draw and will increase the wear and overheating of the wiring and electrical connectors.
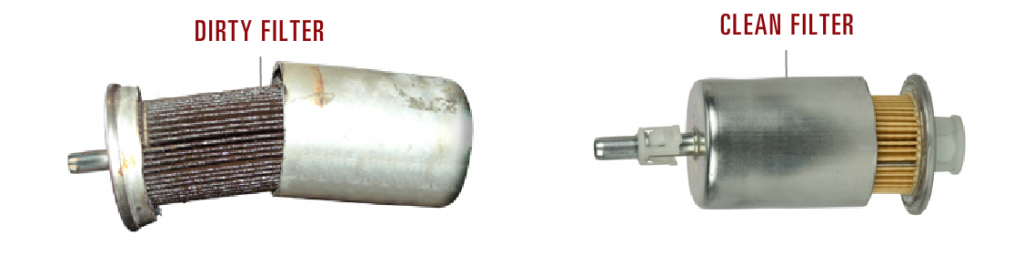
Electrical and Electronic Failure
Fuel pumps are activated by a relay via the computer or directly from the on-board computer.
Safety devices such as fuel cut-offs are integrated to the circuit. These devices are used to cut power to the pump in case of accident and also prevent fuel spillage or fire.
Relays, switches, connectors and splices can all reduce the voltage at the fuel pump and may cause pressure failure.
Lower voltage equals lower pressure and volume, giving you the same symptoms as a defective fuel pump.
Improper Installation
Improper installation can cause all of the above symptoms including fuel leaks, a turned on malfunction indicator light (Check Engine) and noise. Always mark the location of the electrical wiring and tubing. Inspect for proper orientation of the strainer filter in the fuel tank.
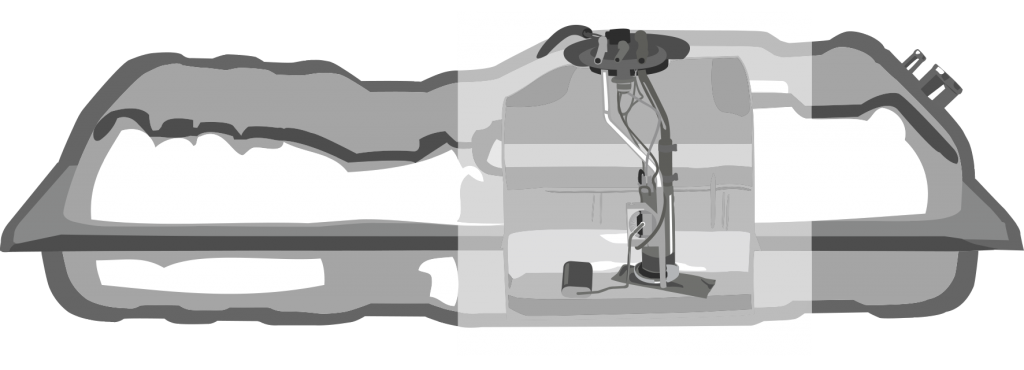
Inspection
Inspect the sender or hanger sealing surface on the tank for damage and corrosion. A new seal or gasket must be installed to prevent fuel leaks. The lock ring must be replaced to ensure proper sealing.
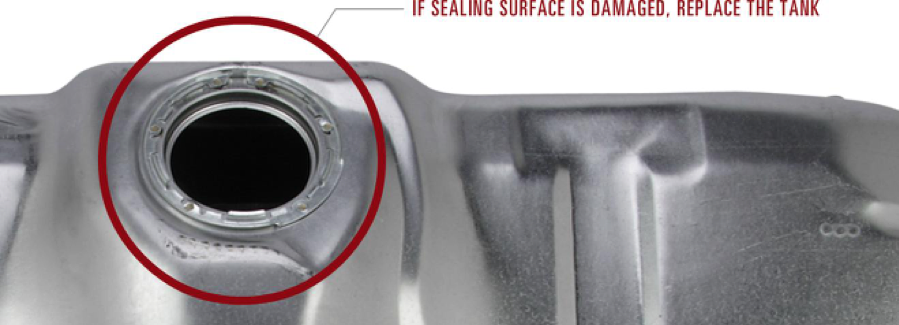
All seals found on hoses, fittings or quick couplers must be inspected and replaced as needed upon reinstallation. Make sure all insulating rubbers between the fuel tank and the body floor are in place. Discarding any insulators without replacing them will emit noise, and the fuel pump could be diagnosed as defective.
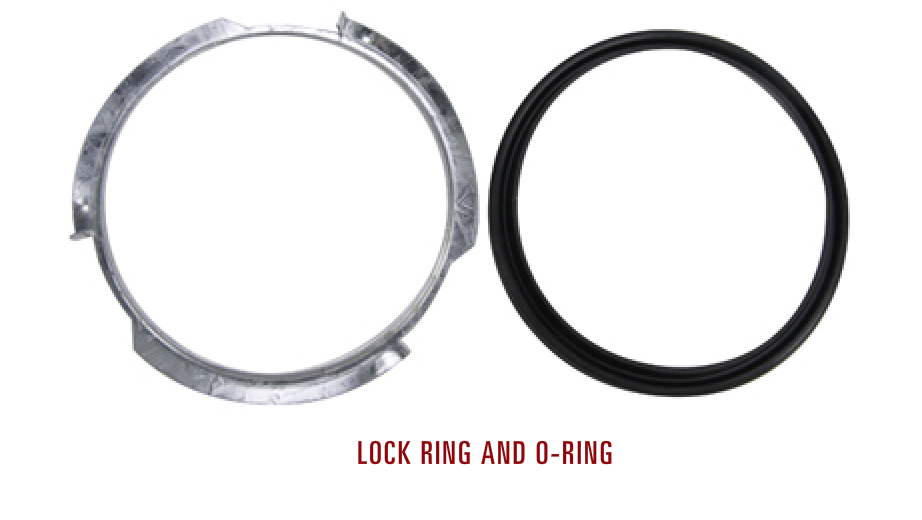
Fuel tank straps must be inspected or replaced if damaged. Newer vehicles have a fuel evaporative system integrity check to ensure that the system is totally sealed or the check engine light will come on.
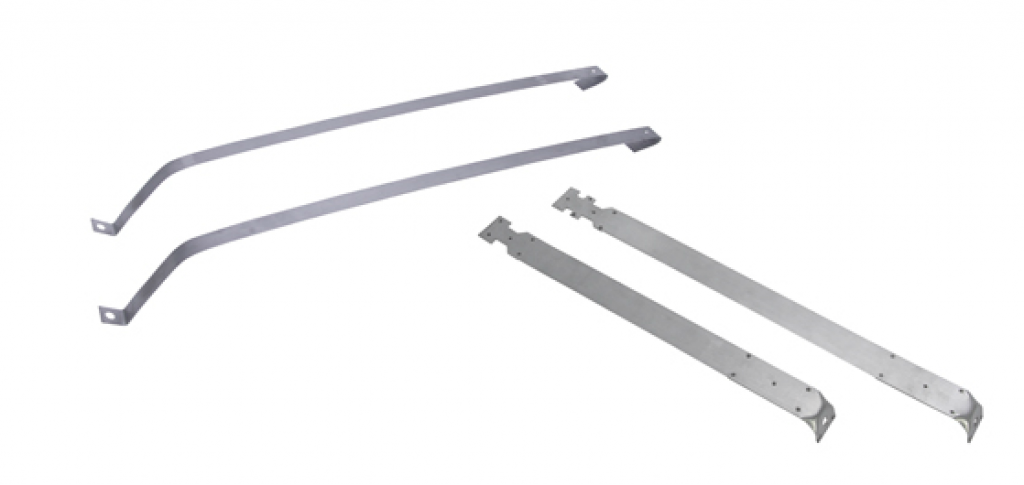