2.4 - Fuel Pressure Control
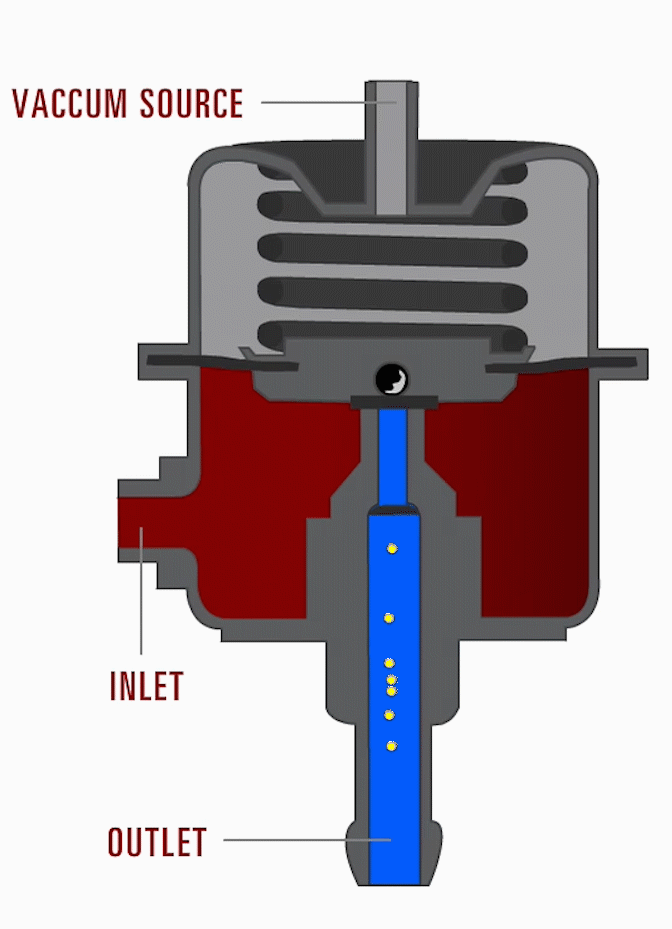
On a return-type system, the fuel pressure is controlled by a regulator. The regulator is located on the fuel injector rail on the engine.
A spring/vacuum diaphragm regulator is used to vary pressure upon engine load. The function of the regulator is to maintain a constant pressure cross the injectors at all times.
A vacuum hose linked to the engine intake manifold allows fuel pressure adjustments.
Excess fuel returns to the tank via the return line.
The pressure in a returnless-type fuel system is constant at all times and is established by a spring preload diaphragm. Excess fuel is bypassed through the regulator and returned to the fuel tank. This design was opted so that no heat-soaked fuel would return from the engine and lower fuel vapors in the tank.
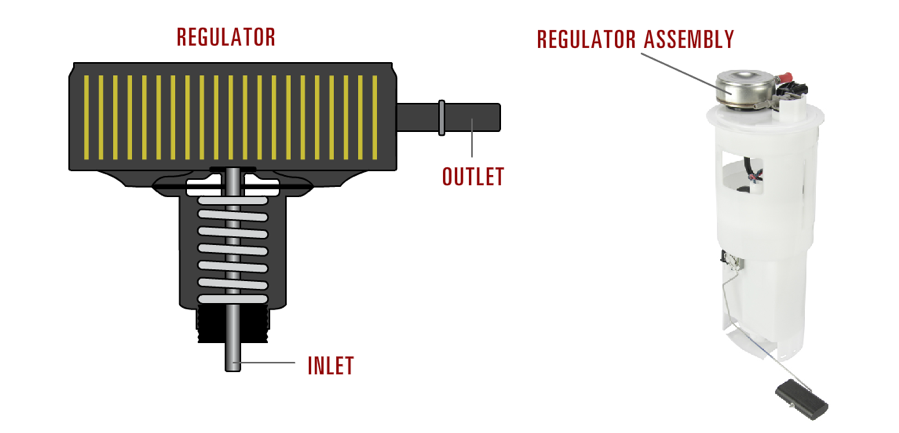
On the mechanical returnless system, the computer simply controls pulse width. The pressure is maintained constantly through all the operating ranges of the engine. When the engine requires additional fuel, the computer varies the pulse width of the injector to compensate for various engine loads.
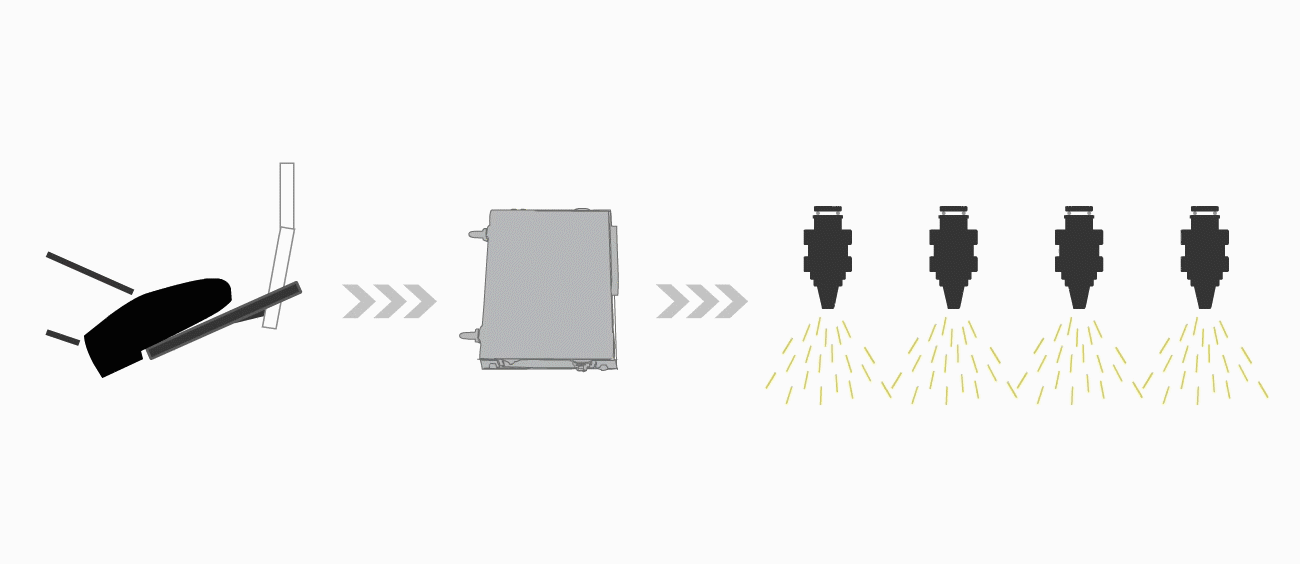
The electronic returnless system incorporates a more sophisticated approach to fuel delivery. Compared to the mechanical returnless system, fuel compensation is achieved by controlling the fuel pump's speed to vary pressure. With this system, the computer must rely on new sensors: the Fuel Rail Pressure sensor (FRP) and the Fuel Rail Temperature sensor (FRT).
These sensors inform the computer about the actual pressure and temperature which in turn controls pump voltage. A module located between the relay and the pump controls thepump's speed. The computer may also increase the fuel pressure to prevent fuel vapour lock when the engine is hot. The fuel module receives signals from the computer and cycles the pump. In addition, fuel pressure reading can now be taken from the scan tool. This does not eliminate the use of fuel pressure gauge testing as the FRP sensor may be at fault.
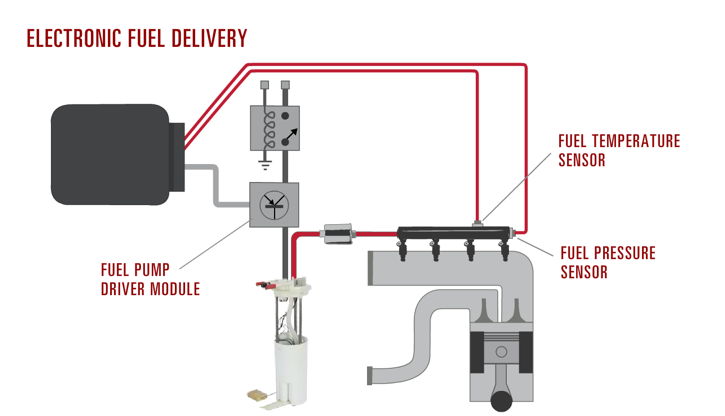